The COVID crisis we all experienced revealed the need for change.
Above all, it was the realization that our industry is heavily dependent on Asian countries. Today, there are many announcements of relocations and investments in new production sites in Europe to cope with this situation. But it's a real challenge to produce in Europe at an acceptable cost.
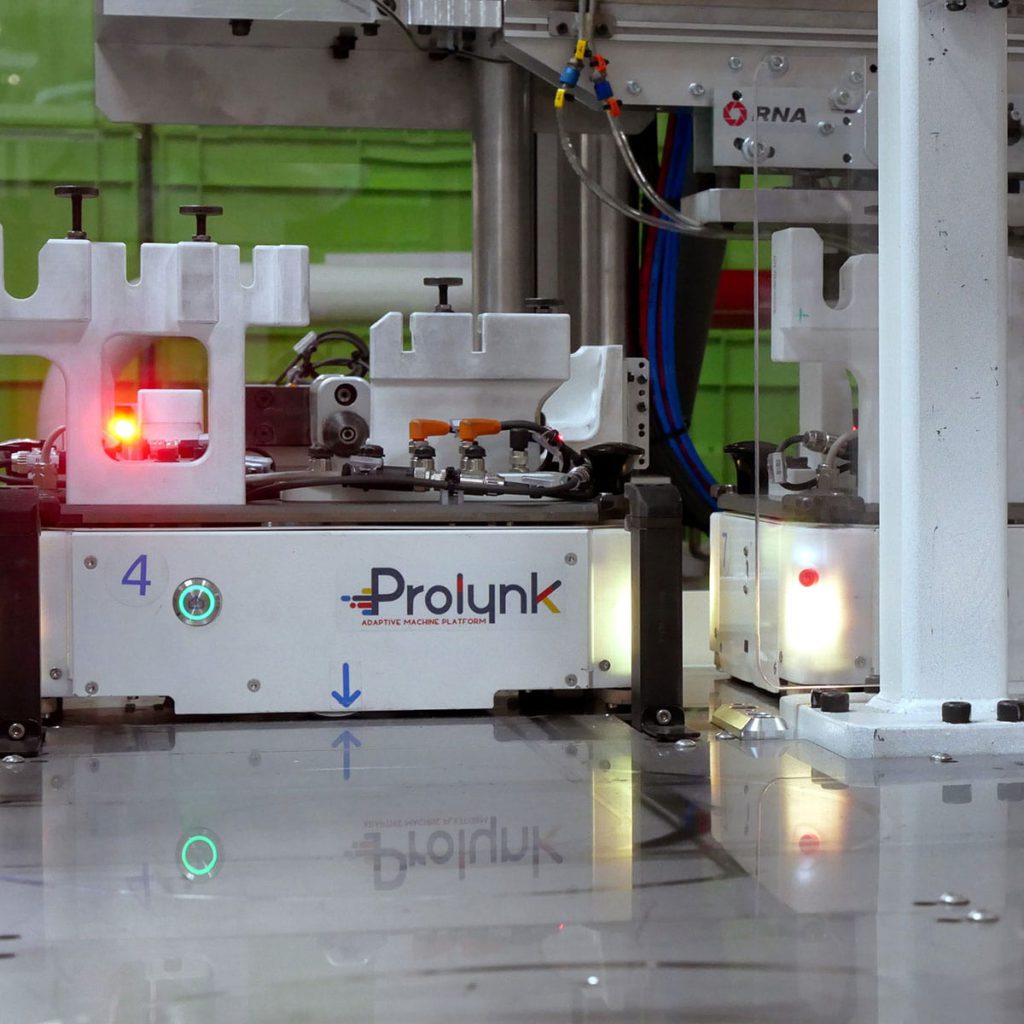
Long before the crisis, the market was undergoing a profound transformation towards a demand for more personalized products, available more quickly. This phenomenon began in textiles, where customers are looking for clothes that reflect their personality and are no longer mass-produced products. The entire value chain and logistics have undergone profound change: regular collection renewal with lower production volumes. To meet this new strategy, production has been relocated to countries such as Portugal, Spain, Morocco… all in a context of controlled costs (less logistics, skilled workers and design-to-cost).
If we take a closer look at the manufacturing industry, it faces the same challenges:
- Controlling the supply chain in Europe.
- Ensuring acceptable production costs.
- Invest in production resources in an uncertain economic climate.
- Finding the right human resources: skills, expertise and sufficient numbers.
- Optimize labor costs by automating production resources.
Assembling in Europe, and particularly in countries with high labor costs, imposes severe industrial constraints. Although automation plays an important role in optimizing production costs, certain operations are difficult to replace by robots. That's why it's important to come up with practical solutions to cope with this situation. It is becoming impossible to think of production tools "as before".
A sequential (conventional) assembly line inherently requires :
- The use of processes at each station: screwing, loading, dispensing, plasma, ….
- Operators are positioned at fixed points.
- Internal logistics suffer from numerous obstacles imposed by the system.
- The size of the equipment requires large production areas.
By its very nature, this type of machine :
- Imposes fixed assembly sequences: no flexibility and difficult (and costly) to re-use.
- Low utilization of all assembly stations: no optimization of process functions possible, and their number limited.
- Large number of operators: impossible to balance workstations.
Competition on the market remains unchanged, and it's always the best who wins!
Transforming your assembly lines with a matrix solution like PROLYNK brings immediate benefits:
- The reuse of process functions enables you to increase the utilization rate and invest more wisely.
- Balancing operator positions saves on line manpower.
- Internal logistics are better managed, no longer a constraint imposed by a sequential system.
- Make better use of floor space and invest in a smaller production site.
- Guarantee the best possible use of your production facilities and adapt them to real market needs.
- Progressive, risk-free investment.
PROLYNK supports your industrial strategy and helps you deal with constraints that go beyond the simple means of production. Our role is to understand your challenges and make your projects possible in Europe.
We have concrete examples to share with you, which illustrate perfectly all the benefits of a new industrial production standard: the Adaptive Machine Platform.
Our teams are available to support you and work with you towards a new industrial approach.
Antonio Sanchez / Commercial Director